在現(xiàn)代電子設備不斷向小型化、輕量化和高性能化發(fā)展的趨勢下,柔性印刷電路板(FPC)憑借其可彎曲、折疊的特性,成為了電子行業(yè)的寵兒。而 FPC 折彎機作為實現(xiàn) FPC 彎折加工的關鍵設備,其背后蘊含的技術原理對于保障 FPC 在各類電子產(chǎn)品中的精準應用起著至關重要的作用。
基于塑性變形的核心工作機制
FPC 折彎機的運作根基,是材料學中常見的塑性變形原理。就如同我們?nèi)粘I钪袕澱劢饘俳z,在施加一定外力后,金屬絲會改變原有形狀并維持新形態(tài),這一現(xiàn)象在 FPC 折彎過程中得到了精準復刻。當 FPC 被放置于折彎機內(nèi),設備會對其施加特定方向和大小的外力。在這個過程中,F(xiàn)PC 材料內(nèi)部的原子結構發(fā)生重排,原本規(guī)則排列的原子晶格在壓力作用下產(chǎn)生滑移和位錯,從而使 FPC 能夠按照預設路徑彎曲變形。
這種塑性變形并非無限制的,F(xiàn)PC 材料本身存在一個彈性極限。一旦外力超出這個極限,材料就會從彈性變形階段進入塑性變形階段,實現(xiàn)性的彎折。FPC 折彎機的技術難點之一,就在于精確控制施加外力的大小與時間,確保 FPC 既能完成所需彎折,又不會因過度受力而損壞內(nèi)部電路結構。
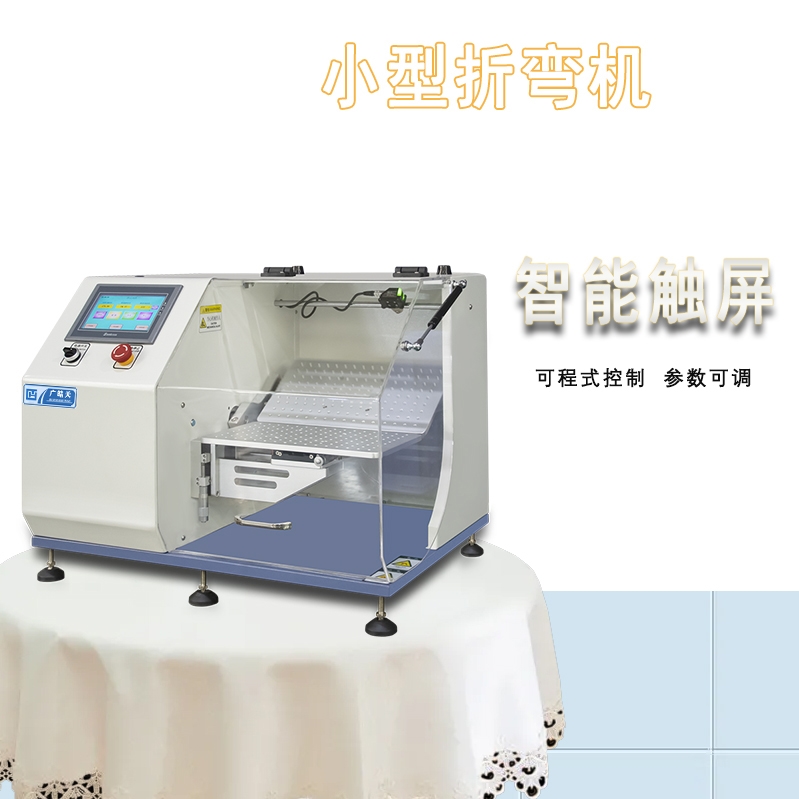
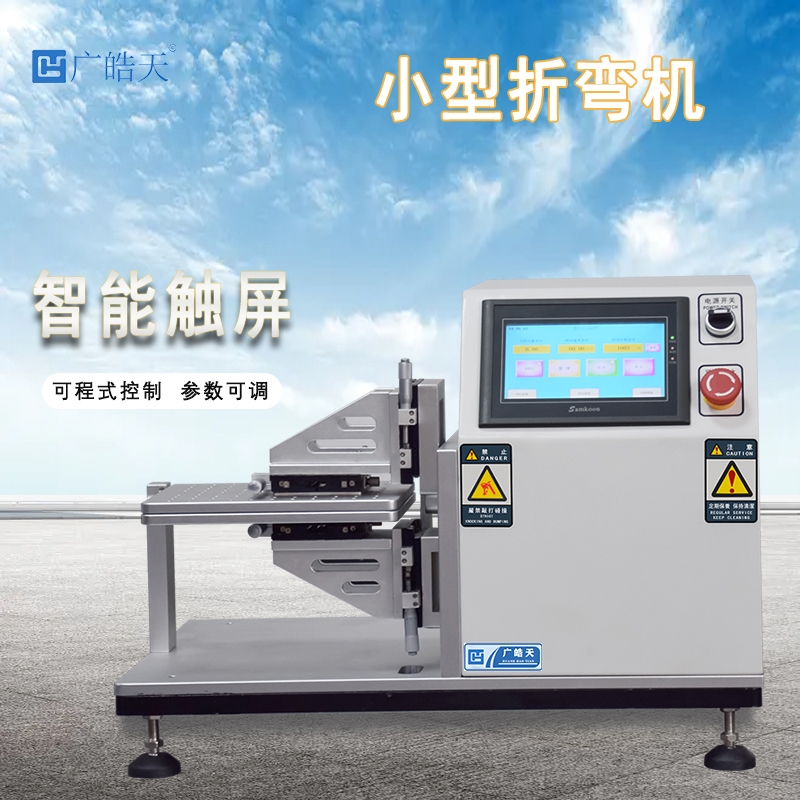
模具:彎折精度的關鍵保障
模具堪稱 FPC 折彎機的 “靈魂組件",其設計精妙絕倫。模具并非隨意打造,而是依據(jù) FPC 的材質(zhì)特性(如不同的絕緣材料、導體材料組合帶來的不同柔韌性與強度)、期望達到的折彎角度以及彎曲半徑等關鍵參數(shù),通過復雜的數(shù)學模型進行精確計算,并借助計算機模擬技術反復驗證后確定的。 以常見的 90 度折彎為例,模具的上下模形狀需要精準匹配 FPC 的截面輪廓,且在折彎過程中,上下模對 FPC 的壓力分布必須均勻。若壓力不均,可能導致 FPC 彎折處一側過度擠壓而另一側彎折不足,影響產(chǎn)品質(zhì)量。對于一些高精度的 FPC 彎折需求,如可穿戴設備中極小半徑的彎折,模具的制造精度甚至要達到微米級,以保證 FPC 在彎折時內(nèi)部電路不受損傷,信號傳輸穩(wěn)定。
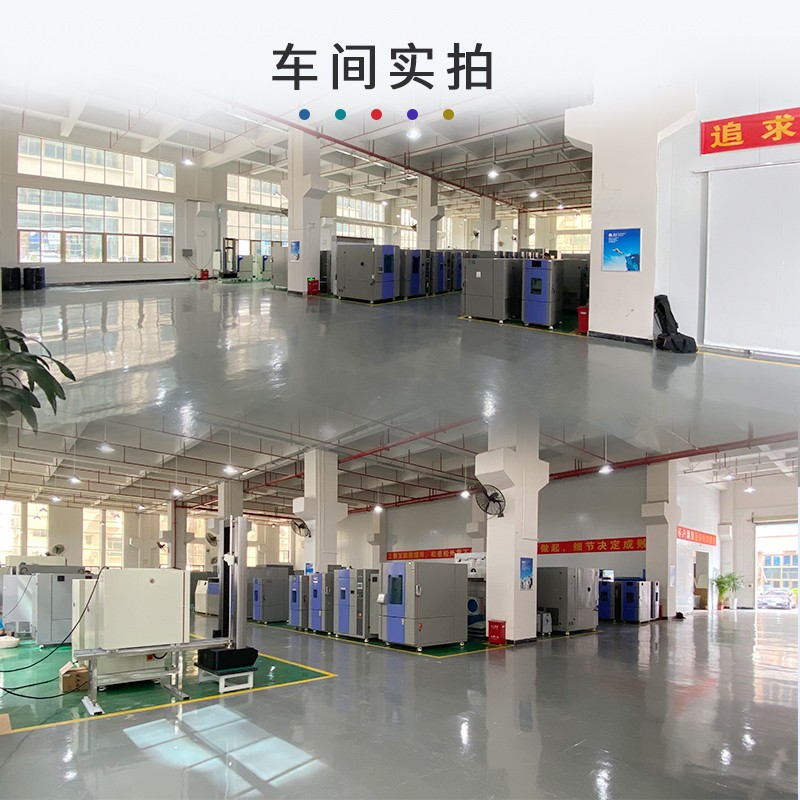
控制系統(tǒng):智能化彎折的 “大腦"
在 FPC 折彎機中,控制系統(tǒng)扮演著 “大腦" 的角色。它不僅要精準調(diào)控模具的運動軌跡和施加外力的大小,還需實時監(jiān)測整個折彎過程中的各項參數(shù)。通過傳感器,控制系統(tǒng)能夠?qū)崟r獲取 FPC 的位置、受力情況以及彎折角度等數(shù)據(jù),并將這些數(shù)據(jù)與預設的理想?yún)?shù)進行對比分析。
一旦發(fā)現(xiàn)實際參數(shù)與預設值存在偏差,控制系統(tǒng)會迅速做出反應,通過調(diào)整電機轉(zhuǎn)速、液壓系統(tǒng)壓力等方式,對模具運動和外力施加進行實時修正。這種閉環(huán)控制機制確保了每一次 FPC 折彎的高精度和一致性。此外,隨著工業(yè) 4.0 和智能制造技術的發(fā)展,現(xiàn)代 FPC 折彎機的控制系統(tǒng)還具備智能化編程功能。操作人員只需在人機界面上輸入 FPC 的材質(zhì)、尺寸、彎折要求等信息,控制系統(tǒng)便能自動生成折彎工藝方案,并控制設備完成操作,大大提高了生產(chǎn)效率和加工精度。